Project
Description
Objectives
Activity plan
The SpaceLAB project has two primary focuses: the development of a test bench for Pyroshock and the development of a test bench for Outgassing.
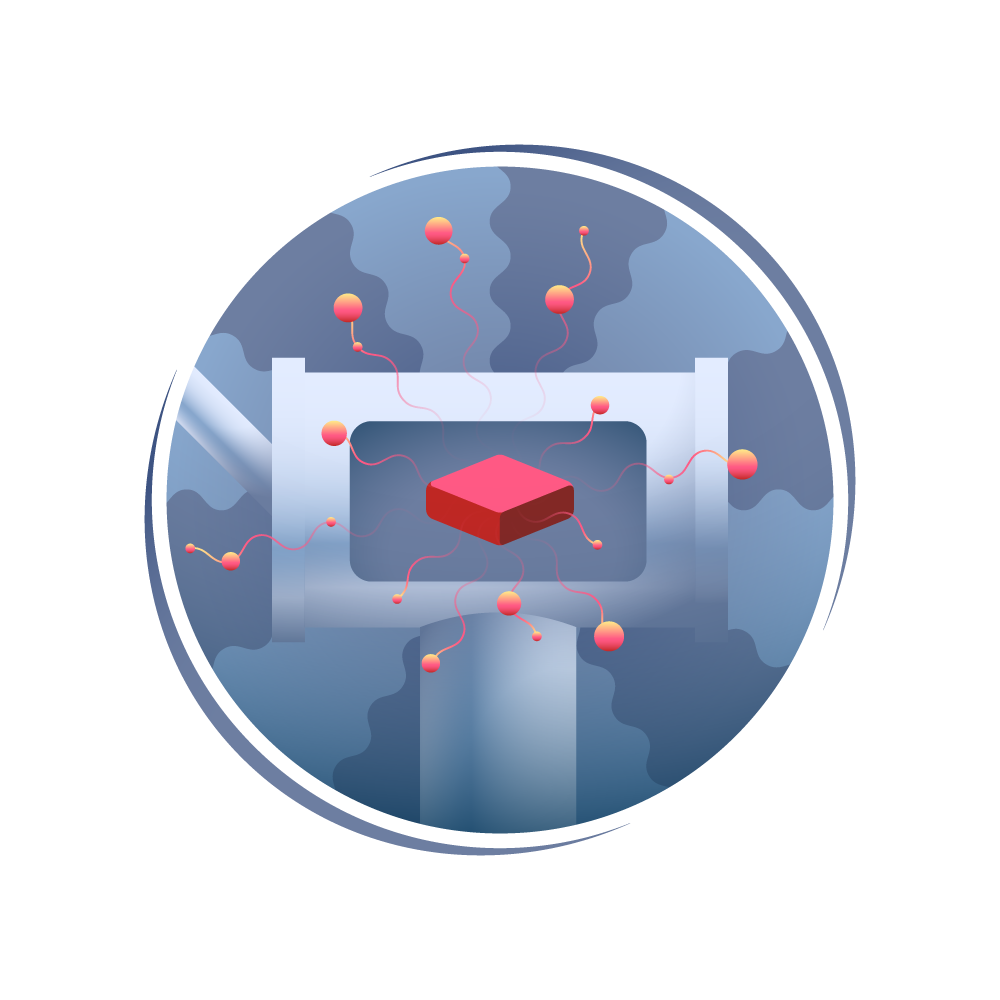
Outgassing tests:
The development of this test bench is based on using "DTM" test equipment to simulate conditions similar to those in the space vacuum. An upgrade to the equipment will be designed, which will include the installation of a TQCM system (Termoelectric Quarz Crystal Micro Balance), the necessary acquisition and cooling systems to conduct the test. Outgassing can cause contamination and affect the functionality of systems so the use of TQCM sensor is essential as it will guarantee precise use in measuring mass changes at the nanogram level and play important role in qualifying the aerospace components.
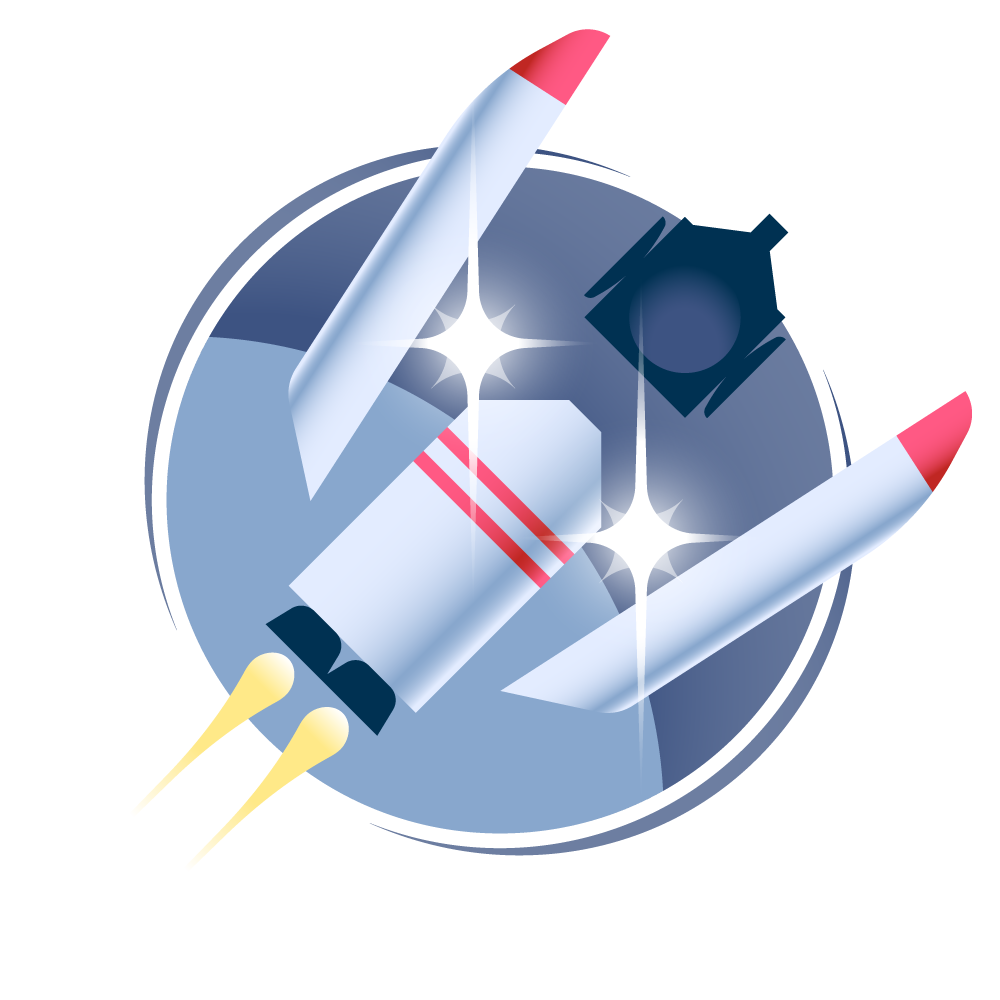
Pyroshock Tests:
Pyroshock is the dynamic structural shock that occurs when an explosion or impact occurs on a structure. Pyroshock testing is of particular relevance to the defense and aerospace industries because it serves to verify the structural and/or functional resistance to vibration occurring during launch phase and/or in the following phases, like structural subsystems separation (e.g., payloads from launch vehicles), deploy appendages (e.g., solar panels). The test bench will be designed, validated on a small scale prototype, realized on full scale and then validated in an industrial environment during the Project development.The first step for the realization of the test bench is the model of the main dynamics of the test to enable the simulation of various experimental setup configurations in a short time, followed by the development of a predictive Pyroshock model, which is essential for equipment design and experimental validation.
Results
Design and build a test bench for Pyroshock tests
Develop and integrate Pyroshock test design and optimization techniques into a single software
Define a new CAx methodology to guide design activities to predict how to modify the design and structure to withstand the required shock during testing
Design and develop the Outgassing test system, implementing a surface contamination measurement device under vacuum conditions with TQCM sensors